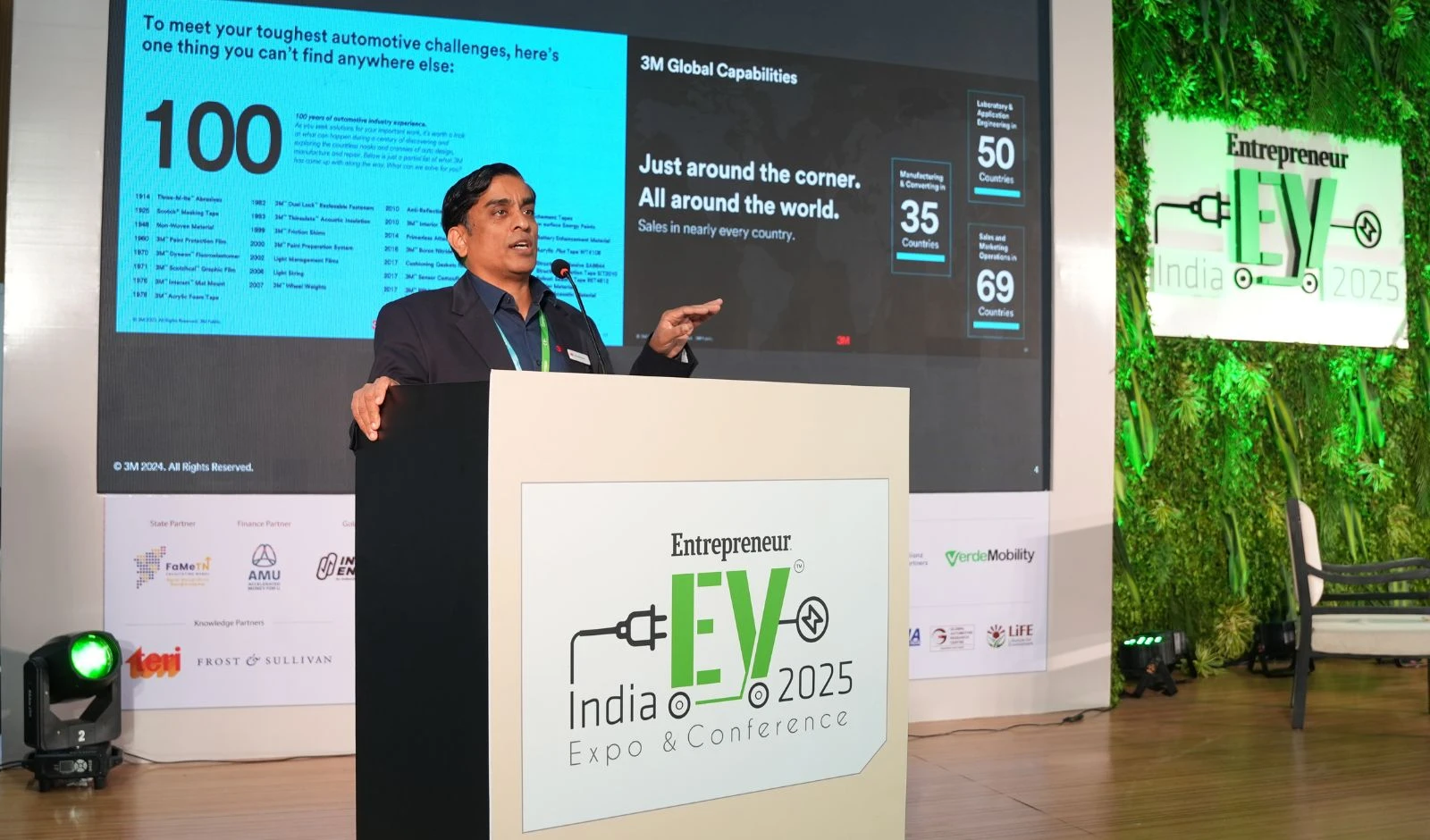
Battery chemistries and instead dove deep into the unseen science that holds electric vehicles together, Manoj Shankar, R&D Head for Industrial Adhesives & Tapes Division at 3M India, highlighted the transformative role of adhesive materials in battery systems at Entrepreneur India EV 2025.
3M, celebrating 100 years in the automotive industry, has been a consistent innovator, contributing over 130,000 global patents, and maintaining a strong footprint with labs in 35 countries and sales in 69. Shankar outlined how the company’s deep expertise in material science, lightweighting, and bonding solutions helps bring together disparate components in electric vehicles, especially in the battery pack.
The Evolution of Battery Pack Design
Battery pack evolution has been influenced by three key trends:
Cell-to-vehicle integration: Removing traditional modules to save weight.
Material transition: Moving from metals to engineered plastics.
Weight & component efficiency: Reducing metal use, increasing energy density.
This evolution demands smart bonding between varied materials like plastics and metals—where traditional bolts or welds fall short.
Adhesive Science: Beyond What Meets the Eye
Shankar explained the crucial difference between adhesion and cohesion—not just how materials stick together, but how the adhesive itself maintains integrity under stress. With 20,000+ products in its adhesive division alone, 3M segments its solutions across a bonding continuum, from thin bonding tapes to structural adhesives.
Thin Bonding Tapes: Used for cell-to-cell bonding, sensor attachment, insulation inserts, etc. These require no thermal curing and are automation-friendly.
Semi-Structural Adhesives: 3M’s innovations like VHB spools and reworkable rope adhesives provide design flexibility, stress relief, and sustainability. Applications include large pack sealing and lift covers.
Structural Adhesives: Offering >2,000 psi strength, these epoxies, acrylics, and urethanes are used for battery floor-to-frame bonding and cover applications. Their design-readiness enables finite element analysis (FEA) with 3M’s Material Data Cards.
Design to Deployment: Full Lifecycle Support
3M supports EV OEMs from design to automation, with facilities in India (Bangalore) and across the globe (St. Paul, Germany, Shanghai). Their tools and material data cards, compatible with simulation platforms like Abaqus and Ansys Workbench, allow faster R&D, fewer physical prototypes, and robust validation.
“You cannot spend 12 months just prototyping when a simulation can be done in a day,” Shankar stated, emphasizing the importance of value engineering and design agility in the fast-evolving EV landscape.
Conclusion
With battery systems becoming lighter, more complex, and safety-critical, 3M’s material science expertise in bonding and sealing is becoming increasingly vital. The company's commitment to reliability, reworkability, and performance positions it as a strategic partner for EV manufacturers aiming to innovate at speed and scale.